
SHEET METAL MACHINERIES
At SG Laser, we specialize in high-performance Press Brake Machines designed for precision bending and metal fabrication. With a commitment to innovation and quality, we provide cutting-edge solutions that enhance efficiency, accuracy, and productivity for industries worldwide. Whether you need a manual, hydraulic, or CNC press brake, our machines are built to meet your toughest requirements.
"Discover reliability, precision, and superior craftsmanship—engineered to shape your success."

High Precision Bending
High Force and Capacity
Press brake machine
precision punching machine
SG Laser offers punching machinery capable of features like creating holes, shapes, or cutouts in sheet metal by applying high force through a punch and die mechanism. It operates using mechanical, hydraulic, or CNC-controlled systems to ensure precision and efficiency.
Commonly used in industries like automotive, aerospace, and construction, punching machines offer fast production speeds, minimal material waste, and the ability to handle various metals, including steel, aluminum, and brass. With features like automatic feeding, multi-tool turrets, and programmable controls, modern punching machines streamline manufacturing processes while maintaining high accuracy.
High Precision and Accuracy
Automatic Material Feeding & Loading
Advanced CNC Control System
-
The CNC control system is at the heart of the press brake's functionality. It enables easy programming of bending parameters, such as angle, length, and speed, directly from a computer interface. Many modern systems come with intuitive touchscreens, graphical displays, and programming aids that simplify operation and improve user experience, reducing setup times and improving overall efficiency.

Flexible Tooling Options
-
Precision press brakes offer a wide range of tooling options to handle various bending tasks. The machine can accommodate multiple tool types such as V-dies, upper and lower punches, and specialized tooling for different bending angles and thicknesses. The quick-change tooling system allows operators to swap tools easily and quickly, minimizing downtime between tasks.
-
Precision press brakes are designed to handle thick metal sheets with substantial force. The machine’s tonnage (force capacity) determines the maximum thickness of the material it can bend. With force capacities ranging from a few tons to several hundred tons, these machines can handle heavy-duty applications, bending thicker materials without compromising accuracy.
High-Speed Bending
-
Modern press brakes are designed for high-speed bending without sacrificing precision. This high speed is achieved through advanced hydraulic or electric drive systems that enable quick, consistent movements. Fast bending cycles lead to increased production efficiency, reducing overall operating time for jobs and making the machine ideal for high-volume production runs.
Integrated Safety Features
-
Safety is paramount when operating precision press brakes, and many modern machines come equipped with a variety of safety features to protect operators. These include light curtains, safety mats, and two-hand controls, which ensure the operator’s hands remain clear of the bending area during operation. Additionally, emergency stop functions and overload protection prevent accidents and equipment damage.
-
The core feature of a precision punching machine is its ability to create highly accurate and repeatable holes and shapes in metal sheets. Advanced CNC (Computer Numerical Control) systems enable precise control over the punching process, ensuring each part is made to exact specifications. This accuracy is particularly critical when producing parts that require tight tolerances for assembly or further processing.
Flexible Tooling Options
-
Precision punching machines are equipped with an extensive range of tooling options, such as punches, dies, and tooling stations, which allow for the creation of various hole shapes, sizes, and patterns. Quick-change tooling systems enable operators to swap between different tools rapidly, optimizing production time for different jobs. Additionally, custom tooling can be designed for unique applications, further enhancing the versatility of the machine.
High-Speed Operation
-
One of the standout features of precision punching machines is their ability to operate at high speeds. Advanced servo motors and hydraulic systems enable rapid punching cycles, ensuring fast production times for high-volume tasks. This feature is vital in industries where time efficiency and large quantities are a priority, such as in automotive and electronics manufacturing.
-
Many precision punching machines come with automatic material handling systems, such as sheet feeders and automatic loading and unloading mechanisms. This automation reduces the need for manual handling and improves the overall speed of production by feeding multiple sheets into the machine in a continuous process. This feature significantly reduces downtime between operations and enhances overall efficiency.
CNC and Programmable Control
-
CNC controls are integrated into precision punching machines to manage the punching sequence, tool changes, and positioning with high accuracy. The programmable control system allows for the easy input of specific design parameters (such as hole size, spacing, and positioning) through a user-friendly interface. This eliminates the need for manual adjustments, reduces operator error, and ensures consistency across production runs.
Multiple Punching Stations
-
Precision punching machines often feature multiple punching stations, allowing for several punches to be executed simultaneously. This multi-station design increases productivity by enabling multiple operations in one pass. The ability to perform various functions, such as piercing, shearing, and notching, within a single cycle helps reduce overall production time and machine setup.
-
Precision press brakes are equipped with advanced CNC (Computer Numerical Control) systems that ensure accurate control of the bending angle, depth, and positioning. This level of control allows for the creation of complex, intricate shapes with tight tolerances. The precision ensures that even the most demanding bending operations are carried out with consistent accuracy every time.
Professional sheet metal machines are essential tools in metal fabrication, allowing precise and efficient customisation of metal sheets for various industrial applications.
These machines come in different types, including hydraulic, pneumatic, and CNC-controlled models, each designed to enhance productivity, accuracy, and repeatability in metalworking processes.
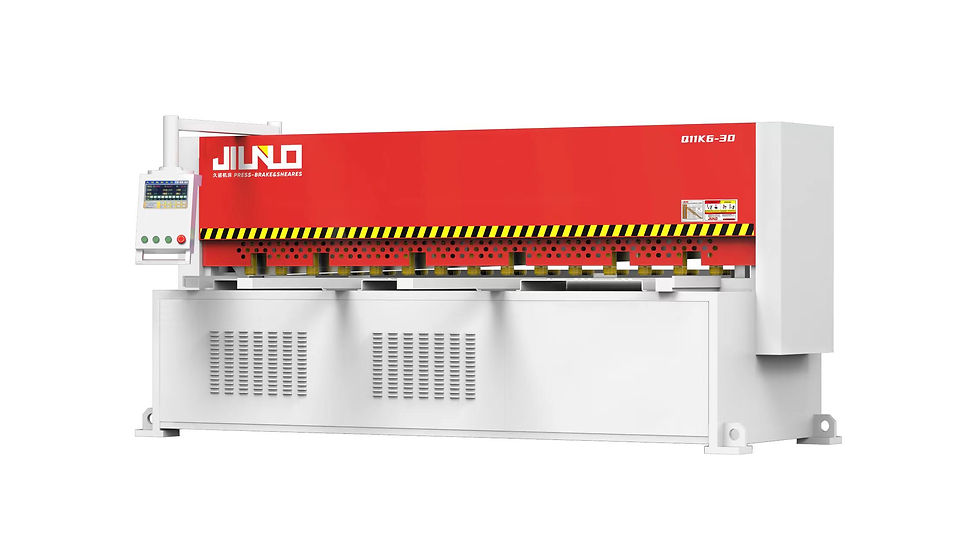

Programmable Control for Automation Clearance
Safety Features
SHEARING MACHINE
At SG Laser, we offer high-performance shearing machines designed for precise, clean, and efficient metal cutting. Whether you need hydraulic, mechanical, or CNC-controlled shears, our machines deliver superior accuracy, minimal waste, and smooth operation for a wide range of materials. Built for durability and reliability, our shearing solutions are perfect for automotive, construction, and metal fabrication industries.
Upgrade your production with cutting-edge shearing technology—precision starts here!
precision V-CUT machine
SG Laser's also specialized in offering precision machinery like a V-Cut machine, also known as a V-grooving machine, is a precision tool used to create V-shaped grooves or channels on materials such as metal or plastic. These grooves are essential for applications like folding, bending, or jointing components in various industries such as manufacturing, construction, and product assembly.
Accurate Angle Control
Minimal Burr Formation and Clean Edges
Automatic Material Alignment and Feeding System
Energy-Efficient Operation
-
Shearing machines are typically powered by either a hydraulic or mechanical drive system.
-
Hydraulic drive systems provide more control over the cutting force, allowing for smooth, consistent cuts across various material thicknesses.
-
Mechanical drive systems, which use flywheels and clutches, are ideal for high-speed operations and often provide faster cycle times. Both systems ensure high cutting force, ensuring clean cuts with minimal deformation.
-
Modern precision shearing machines are equipped with programmable control systems, often CNC-based, to allow for automation in cutting tasks. These controls enable operators to program the machine for precise lengths, angles, and quantities of cuts. Automatic sequencing can be used to perform a series of cuts without the need for manual adjustments, increasing efficiency and reducing the likelihood of operator error.
Safety is a top priority in precision shearing machines, which are equipped with several advanced safety features to protect operators and minimize accidents:
-
Safety Light Curtains: Sensors that stop the machine’s operation when the operator’s hands or body are detected within a dangerous area.
-
Two-Handed Operation: Prevents operators from being near the cutting blade during operation by requiring both hands to be placed in designated safety areas.
-
Emergency Stops: Easily accessible buttons that immediately stop the machine in case of emergency situations.
-
Anti-kickback Mechanism: Prevents the material from being thrown back after the shear has cut through it, improving safety during operation.
Precision Roller Feeding System
-
A precision roller feeding system ensures that the material is moved into the cutting area with high accuracy. The rollers ensure smooth and stable feeding, preventing the material from shifting during the cutting process. This contributes to achieving consistent cut lengths and reduces material waste caused by misalignment or shifting.
-
The V-cut machine allows for precise control over the angle of the cut, which is crucial for fabricating parts that need to be bent or welded at specific angles. The machine typically supports a range of angle settings, such as 30°, 45°, and 60°, with the flexibility to accommodate custom angles. The angle adjustment mechanism ensures that the cutting process is highly accurate, enabling manufacturers to achieve tight tolerances and meet specific design requirements.
CNC Control for High Precision
-
Modern precision V-cut machines are often equipped with CNC (Computer Numerical Control) systems that enable highly accurate and automated cutting. CNC technology ensures repeatable, consistent cuts, minimizing errors caused by manual adjustments. Operators can program cutting paths, angles, and depths through the CNC interface, and the machine can execute these commands autonomously, optimizing productivity and reducing setup times.
Fast Cycle Time for Increased Productivity
-
V-cut machines are designed to operate at high speeds while maintaining cutting precision. The fast cycle time ensures that materials are processed quickly, making it ideal for high-volume production environments. Combined with automated feeding and cutting processes, the machine minimizes downtime between cuts, leading to greater efficiency and output.
-
The automatic material feeding and alignment system ensures that the material is positioned accurately before each cut. This feature minimizes human error, ensuring that the sheets are aligned correctly for each V-shaped cut. Some machines even incorporate automatic clamping mechanisms to hold the material securely in place during the cutting process, preventing movement and ensuring consistent results.
-
One of the key benefits of a precision V-cut machine is its ability to produce clean, burr-free edges. Unlike traditional cutting methods that may leave rough or jagged edges, the V-cut machine ensures that the material is cut with minimal deformation and no burrs. This results in better-quality parts, reducing the need for secondary finishing processes and saving time and cost in production.
-
Precision V-cut machines are designed with energy efficiency in mind. Electric-driven systems are typically more energy-efficient than hydraulic systems, and advanced drive technologies ensure that the machine uses power efficiently, reducing energy costs over time. Additionally, the machine is designed for optimal energy usage, which is essential in reducing the operational costs of large production facilities.
-
Cutting force, measured in tons, refers to the amount of pressure required to shear a specific thickness of material. Precision shearing machines come in various tonnage options, ranging from smaller machines for lighter materials to heavy-duty models capable of shearing thick plates of metal. The machine's tonnage is determined based on the maximum material thickness and strength it can handle, making it suitable for different manufacturing needs.
Hydraulic or Mechanical Drive System
Multiple Cutting Modes
Cutting Force and Tonnage
-
Precision shearing machines often feature multiple cutting modes to accommodate different tasks. Some common modes include:
-
Single Cut: Ideal for cutting individual sheets or plates to a desired length.
-
Continuous Cut: Used for cutting long sheets or for jobs requiring continuous cutting without frequent stops.
-
Step Cut: Involves cutting in incremental steps for materials that may need multiple passes for thicker sections. These versatile modes enhance the machine’s flexibility, allowing it to handle both simple and complex cutting jobs.